REAMING TECHNIQUE
The number one problem call we get from customers is about bushing fitment. The number one cause of these calls is improper reaming. After much research and countless hours on the phone, we've narrowed the problems down to three main causes: drill speed, lubrication, and aluminum buildups. Variations on any of the three WILL change the bore size. Turn the reamer slower, you'll make a smaller hole. Faster will be larger. Use ATF or penetrating oil instead of cutting fluid and the bore WILL be larger. Put a little lube on the tool and call it good; the bore WILL be larger.
​
All of these different factors play into the final size of the bore that you ream, and all of the information on this page can be directly applied to all aluminum reaming in transmission applications, regardless of manufacturer or application. Ream a valve body AFL bore with an electric drill shoved through on high with just a little bit of ATF squirted into the bore before you start and that valve will drop right in. You might not be too impressed with your vacuum test results though. Do that same bore with the same reamer by hand with zero pressure in a parts washer tank continuously pumping lube and suddenly that valve won't even drop into your new bore.
​
Because reaming technique can vary so much from person to person (and let's be honest here, from day to day with the same person) we spent a considerable amount of time developing a consistent, repeatable technique that can be easily duplicated in any shop environment. All of our bushings are precisely specified off of the bore that each specific tool makes in it's specific transmission case. Every bushing (not just a production sample) is air gauged at the machine shop, than hand checked here before being shipped. If you follow the information found on this page and in your instructions, your bushing will have plenty of crush (pressure generated from the bushing being marginally larger in diameter than the bore's outside diameter) and you will spend virtually no time resizing to fit your servo pin.

DRILL SPEED
Explaining how drill speed affects bore diameter and bushing fitment is really simple. A faster drill makes a larger hole. The larger the bore, the less crush on the bushing. Less bushing crush means that the bushing may install too freely, and that it won't seal as effectively on the servo pin. Conversely, reamer speeds that are too low will make an under-sized bore. Side effects include hard to install bushings and pins that don't slide freely and require much re-sizing.
​
This is probably the single biggest cause of tech calls. Many technicians have it in their heads that reamers must be turned by hand. This is simply not true. It's also extremely inconsistent. The reality is that if you put the same tool in three different peoples hands, you will get three different speeds. Make it 3:00 pm on Friday afternoon with a customer calling and you'll have three completely different speeds. Add to this the fact that it is completely impossible to maintain a constant, consistent speed while reaming through the entire bore, and you'll understand why we don't recommend reaming with our tools by hand.
​
Aside from hand reaming, other technicians try to use electric drills. While most electric drills are definitely capable of generating the torque necessary to ream the entire bore, the problem comes in when you try to control the speed of the drill. Most electric drills do not have a published speed for their different gear settings published on the drill, so most of the time the user will try to "eyeball" the speed the drill is turning at. They then vary the speed by feathering the trigger. This turns into a run of, "too slow, more trigger. Too fast, less trigger. Too slow, more trigger," and so on. This is obviously a very inconsistent way to ream, and can create bores that randomly seem spontaneously too tight or too loose.
We develop all of our tools around a bore cut with an unregulated gear reduction pneumatic drill. Our tools are specifically developed off of the older Snap-On PDR-5A and have been extensively tested with it's replacement PDR-5000A. Our recommended reamer speeds are developed off of these drills and their published free speed of 500 RPM (PDR-5A) and 490 RPM (PDR-5000A).
DO NOT EXCEED 500 RPM
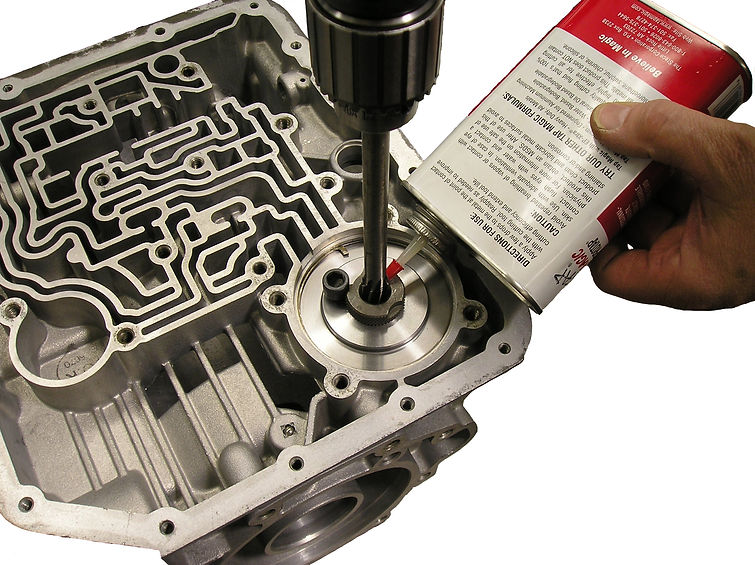
LUBRICATION
Lubrication plays a big part in proper bore reaming. Using improper or inadequate lubrication will lead to over-sized bores and excess aluminum build ups on the reamers. Remember that even with the right lubrication, using too little lubrication will create the same issue.
​
We Recommend Tap Magic for Lubrication.
Make sure to keep a STEADY STREAM of cutting oil on the tool the ENTIRE time you're reaming.
​
MSC #00261933
800-645-7270
ALUMINUM DEPOSITS
Aluminum takes a long, long time to dull tool steel. However, the reamer does collect aluminum on it's cutting edges every time it's used. This phenomenon is not limited to our products. Check any cutting tool in your shop. These "build ups" of aluminum effectively become the new cutting edges. These build ups obviously do not cut as well as the tool steel and are also larger than the original diameter of the reamer. Translation- a larger bore that was a lot harder to cut.
To combat these build ups, we offer a special stone. The stone fits between the flutes of the reamer and cleans the cutting edges up quite nicely. We recommend using the stone on your reamers every time you use the tool.
